CP&A Urges Crane Industry to Better Utilize Heat Straightening
Casper, Phillips & Associates Inc. (CP&A) has advised the crane industry not to overlook heat straightening as a method of repair when structural beams or columns are damaged.
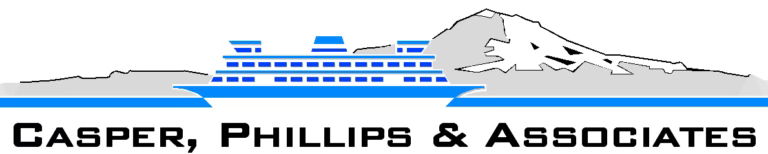
Heat straightening is the ideal solution when a beam or column has plastically deformed — but does not have significant crack formation. It has been used to repair ship-to-shore container crane booms, where failure led to the boom up limit switch not being activated, causing the boom to bend. Heat straightening is not for situations where cracks form because of high-cycle fatigue.
CP&A — the company offers a wide variety of services, including specification, design, manufacturing review, modification, and accident investigation — is filling a gap in typical college curriculum by passing knowledge about this repair procedure to its own engineers, and wider industry.
If an engineer is not familiar with the art of heat straightening, they might have heard of flame straightening or heat curving, which are just different names for using the process of thermal upsetting to change the shape of steel. Heat straightening and heat curving are recognized by the American Institute of Steel Construction (AISC), the American Association of State Highway and Transportation Officials (AASHTO), and the American Welding Society (AWS).
Regardless, industry trends indicate a more common repair procedure is to cut out and replace the deformed steel, even if this may not be the most economical or quickest solution depending on the location or extent of the damage. Patch or lap plates are also commonly used to reinforce damaged areas.
Notably, many engineers are only a few steps away from more wholesale utilization of heat straightening, in that most will understand the science behind deformation and yield stress, which are the building blocks to the concept. Elastic deformation occurs when a load is applied to a piece of steel and the steel returns to its original shape when the load is removed. Plastic deformation is permanent deformation of the steel. Permanent deformation is when the steel is loaded and does not return to its original shape when the load is removed. Yield stress is the amount of stress a piece of steel can withstand before it permanently (plastically) deforms.
Richard Phillips, mechanical engineer at CP&A, said: “We’re not pushing heat straightening lightly. It is an art form and rather niche, and not a very common process in most industries. Further, thermal upsetting should only be performed by a highly trained and qualified tradesperson.”
Phillips explained that, sometimes, curved surfaces and beams are intentional. They may be manufactured using thermal upsetting. For example, thermal upsetting was utilized to create the double curvature legs for the Seattle Space Needle. It can also be used to control weld distortions for higher precision assemblies or to create cambers in beams.
“Typically, in cranes,” he continued, “We are using it to repair damaged areas that were bent, and we are straightening them out. In those cases, we call it heat straightening, but it still falls under the general category of thermal upsetting. As I often simplify, all heat straightening is thermal upsetting, but not all thermal upsetting is heat straightening.”
Heating up a small area
Some engineers think thermal upsetting is hot bending or hot rolling, but these are completely different processes. For hot bending and hot rolling, the entire piece of steel is heated up. Thermal upsetting only heats up a small area and uses lower temperatures than what would be considered to be hot in the steel industry.
Typically, hot rolled steel is processed at over 1,700°F (925°C). Depending on the grade of steel, thermal upsetting is performed in the 700°F to 1,200°F (370°C to 650°C) range. Common structural steel for cranes is ASTM A572; the maximum thermal upsetting temperature for A572 is 1,100°F.
“At these temperatures the steel should be a very dull and dark red. If the steel turns orange, too much heat has been applied. For hot rolling and bending it is common for the steel to be orange,” said Phillips.
Prior to heat straightening, a structural engineer will design a temporary support that will divert the load around the area being repaired. CP&A designs these supports and, depending on the importance of the structure, a civil or structural engineer will be assigned to supervise the repair. The load between the undamaged sections is transferred through these temporary struts. It is common to have hydraulic jacks attached to the struts, which help adjust the lengths to continue diverting the load around the area being repaired as the process progresses.
Phillips said: “The jacks can be used to apply a limited load to the damaged area. The basic mechanism of heat straightening is to create plastic flow through applying heat in specific patterns to gradually straighten the steel. External force is not the primary mechanism of straightening. Using thermal expansion as the primary mechanism helps maintain the material properties.
“The heat is typically applied by an oxyacetylene torch with special tips to help the worker control the heat. Controlling the temperature is one of the most important parameters — it is also one of the most difficult, which is why the skill of the tradesperson is extremely important.”
Evidence points to heat straightening being more economical when a structural beam or column has plastically deformed, provided it does not have significant cracking. Heat straightening may not be applicable in cases where significant brittle fracture is present. Additional situations that may complicate the applicability of heat straightening include material degradation such as significant corrosion, or exposure to a high temperature such as a fire when the damage occurred. An experienced engineer can determine the applicability in cases where these items are present.
- The American Association of State Highway and Transportation Officials (AASHTO) has published a technical report (FHQA-IF-08-999) that goes deeper into heat straightening science.
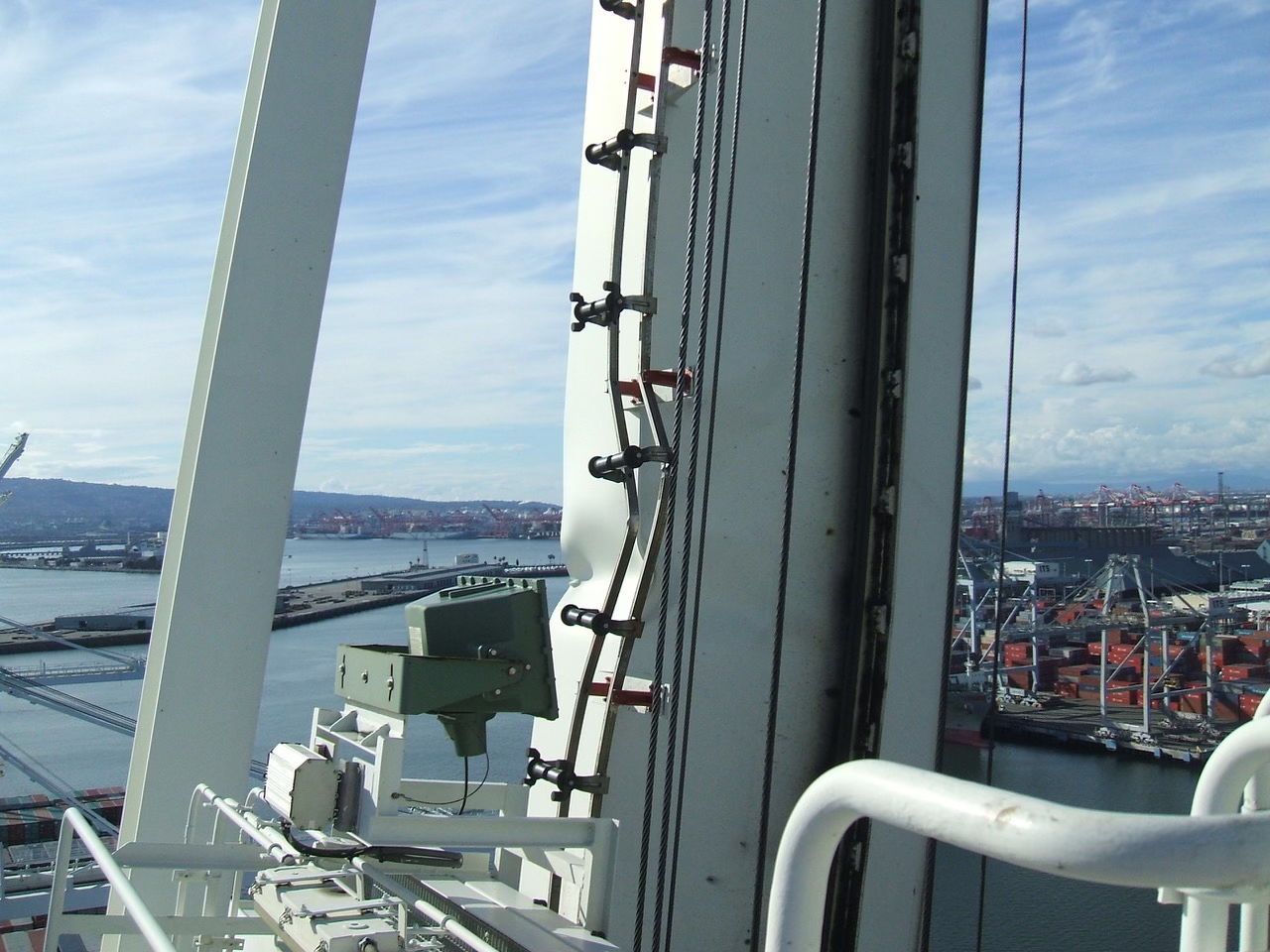
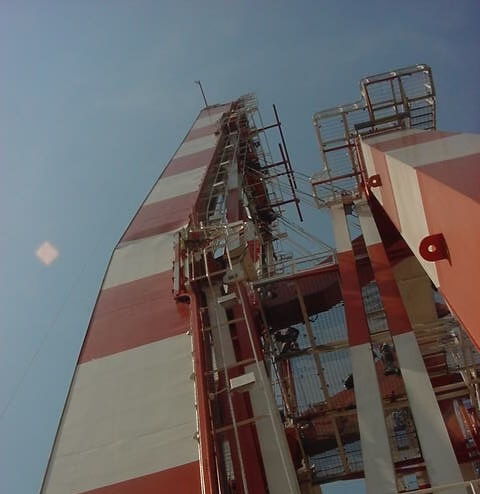
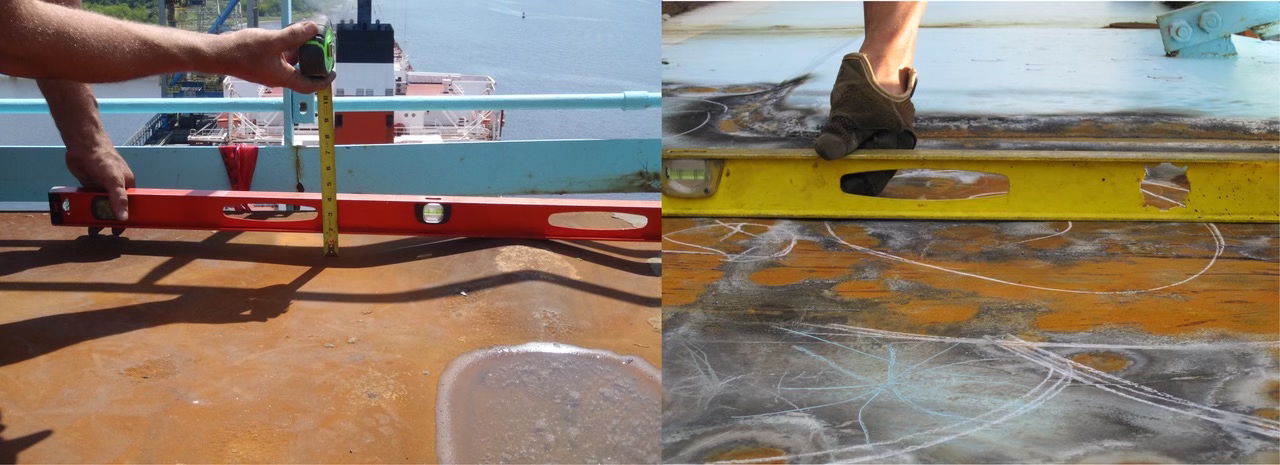
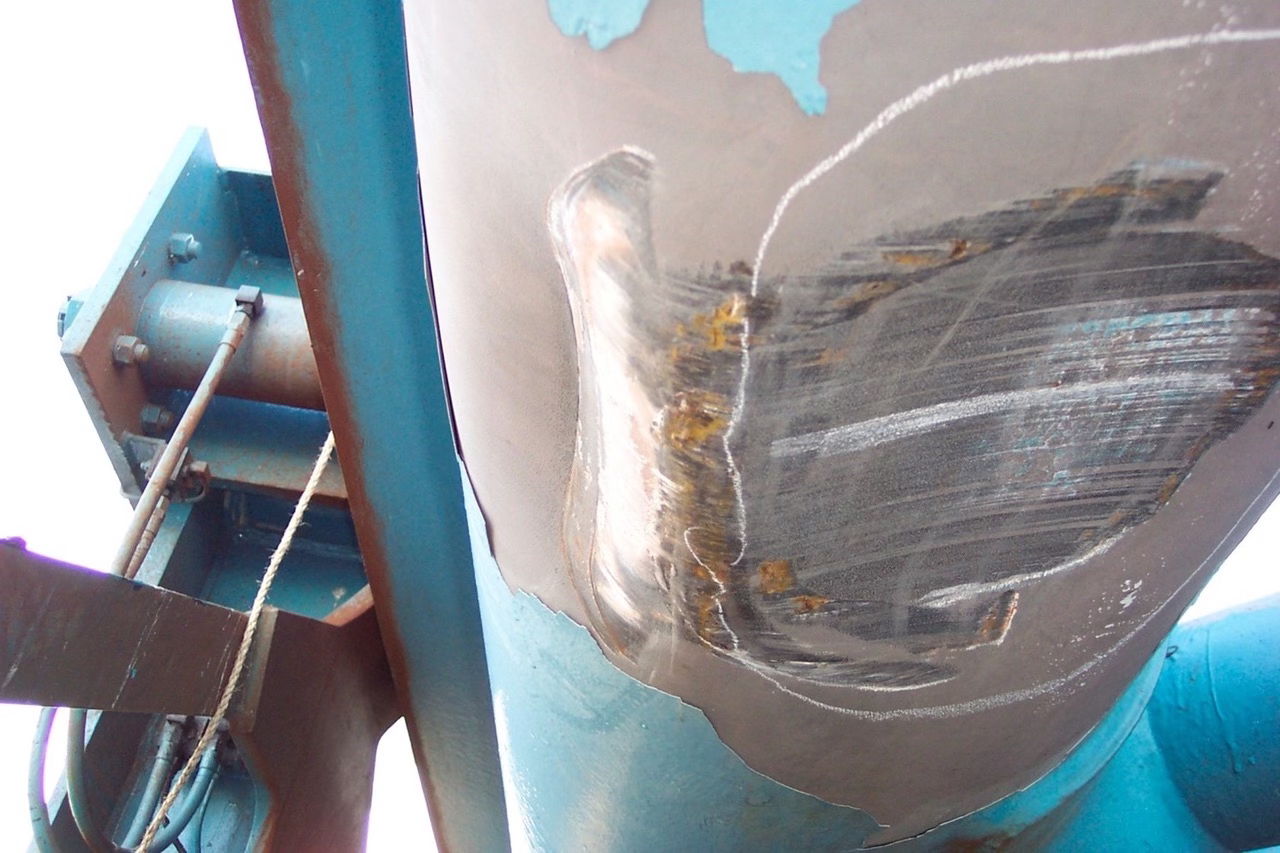

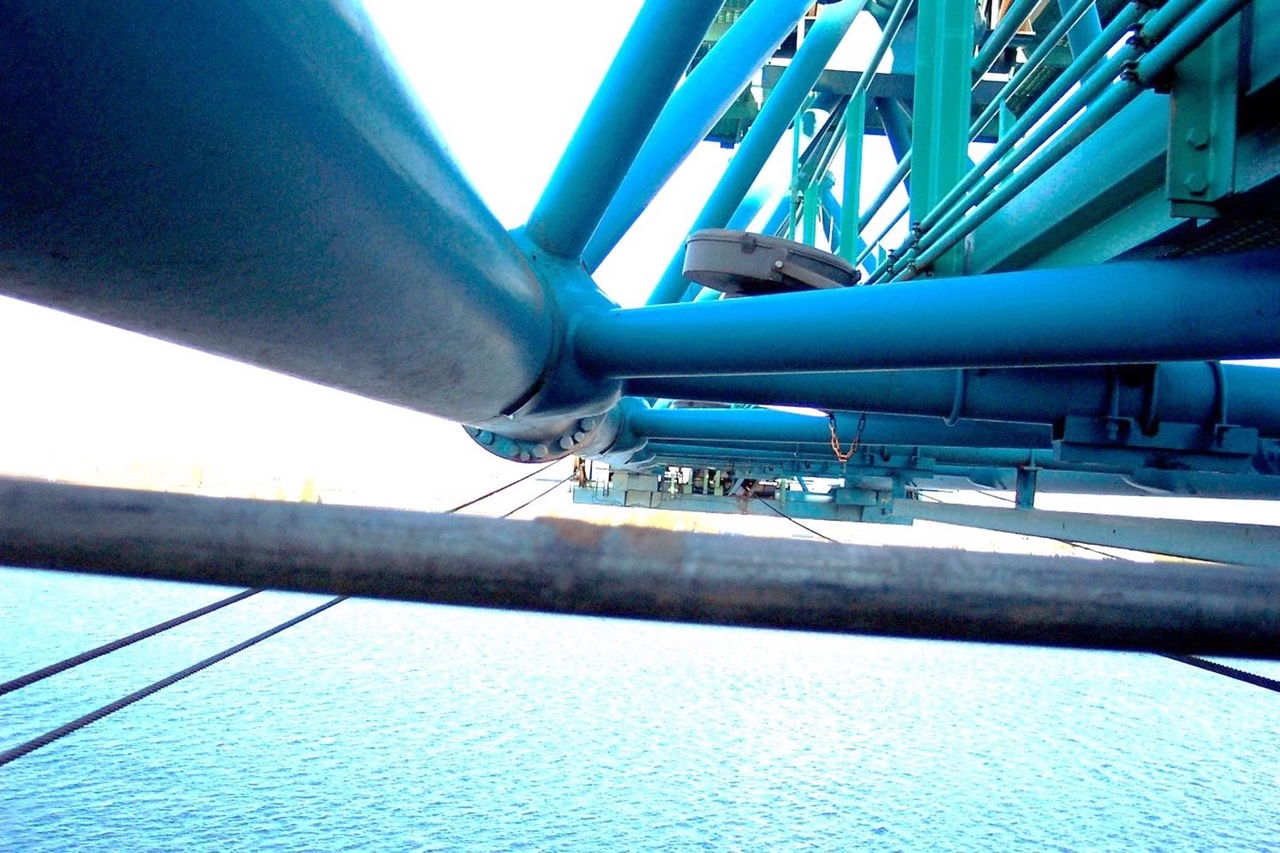
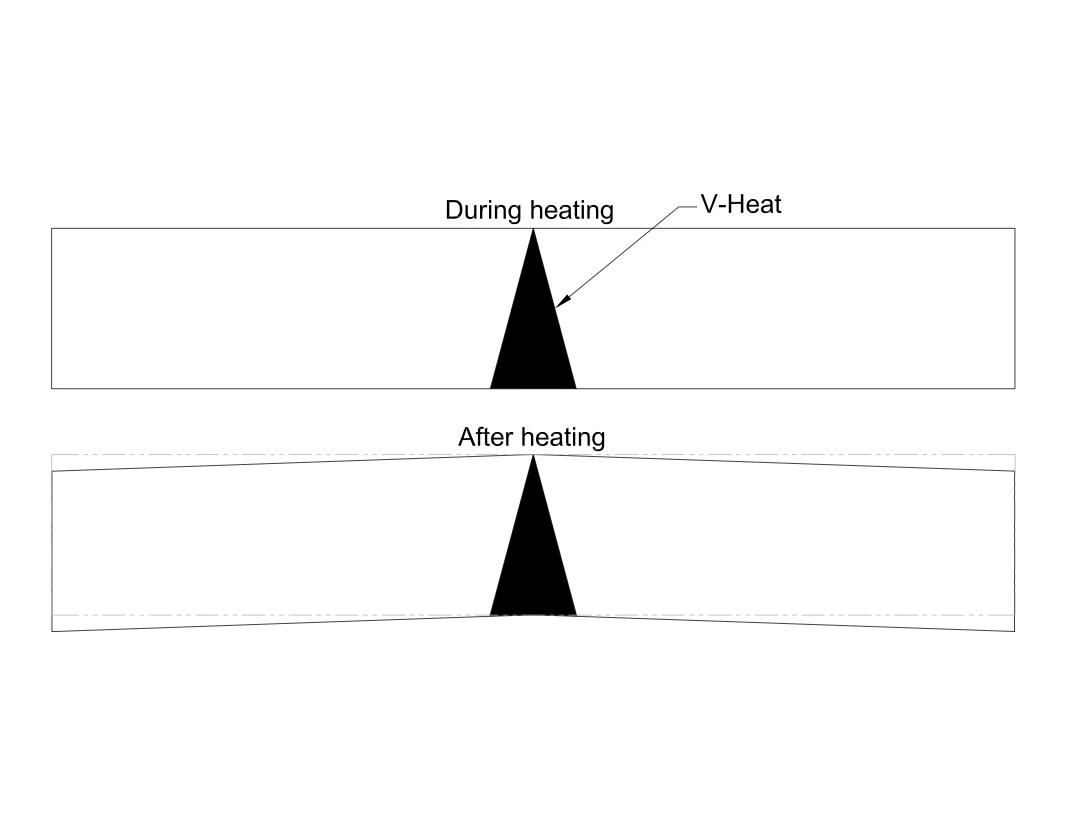